Eisen ist ein Element, das jedem Menschen auf unserem Planeten bekannt ist. Und daran ist nichts Überraschendes. Tatsächlich ist diese Komponente in Bezug auf ihren Geh alt in der Erdkruste (bis zu 5%) am häufigsten. Allerdings befindet sich nur ein Vierzigstel dieser Reserven in entwicklungsfähigen Lagerstätten. Die wichtigsten Erzminerale des Eisens sind Siderit, braunes Eisenerz, Hämatit und Magnetit.
Herkunft des Namens
Warum hat Eisen diesen Namen? Wenn wir die Tabelle der chemischen Elemente betrachten, dann ist diese Komponente darin als "Ferrum" gekennzeichnet. Es wird als Fe abgekürzt.
Laut vielen Etymologen kam das Wort "Eisen" aus der protoslawischen Sprache zu uns, in der es wie zelezo klang. Und dieser Name stammt aus dem Lexikon der alten Griechen. Sie nannten das heute so berühmte Metall "Eisen".
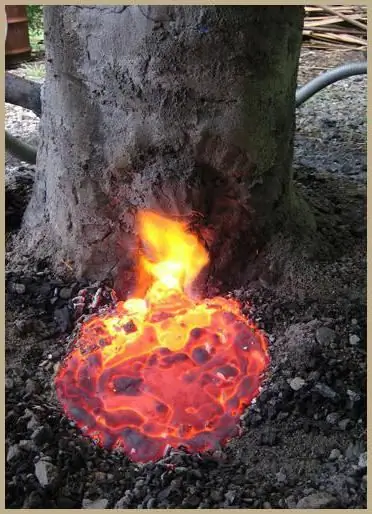
Es gibt noch eine andere Version. Ihr zufolge kam der Name "Eisen" aus dem Lateinischen zu uns, wobedeutete "sternenklar". Die Erklärung dafür liegt in der Tatsache, dass die ersten von Menschen entdeckten Proben dieses Elements aus Meteoriten stammten.
Eisenverbrauch
In der Geschichte der Menschheit gab es eine Zeit, in der die Menschen Eisen mehr schätzten als Gold. Diese Tatsache ist in Homers Odyssee festgeh alten, die besagt, dass die Gewinner der von Achilles arrangierten Spiele zusätzlich zu Gold ein Stück Eisen erhielten. Dieses Metall war für fast alle Handwerker, Bauern und Krieger unverzichtbar. Und es war der große Bedarf, der zum besten Motor für die Herstellung dieses Materials wurde, sowie weitere technische Fortschritte bei seiner Herstellung.
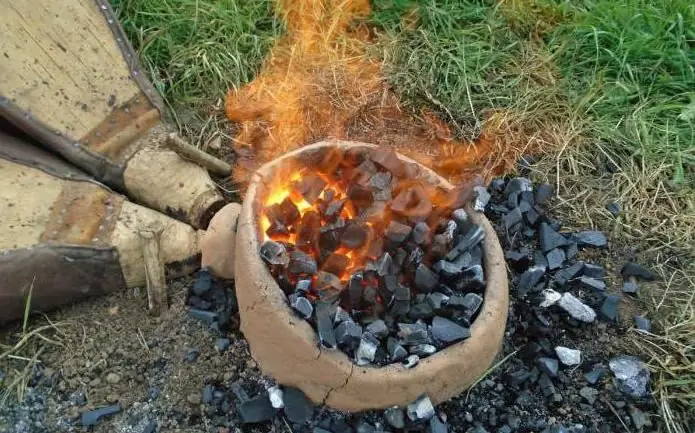
9-7 cc. BC. gilt als die Eisenzeit in der Menschheitsgeschichte. Während dieser Zeit begannen viele Stämme und Völker Asiens und Europas, die Metallurgie zu entwickeln. Eisen ist jedoch auch heute noch sehr gefragt. Immerhin ist es immer noch das Hauptmaterial für die Herstellung von Werkzeugen.
Käseprodukt
Was ist die Technologie zur Herstellung von Bloom-Eisen, mit deren Gewinnung die Menschheit zu Beginn der Entwicklung der Metallurgie begann? Die allererste von der Menschheit erfundene Methode hieß Käseherstellung. Darüber hinaus wurde es 3000 Jahre lang verwendet, ohne sich von der Zeit des Endes der Bronzezeit bis zum Zeitraum bis zum 13. Jahrhundert zu ändern. Der Hochofen wurde nicht in Europa erfunden. Diese Methode wurde roh genannt. Hörner für ihn wurden aus Stein oder Ton gebaut. Manchmal dienten Schlackenstücke als Material für ihre Wände. Die letzte Version der Schmiede von innen warbeschichtet mit feuerfestem Ton, dem zur Verbesserung der Qualität Sand oder Hornschrot zugesetzt wurde.
Was macht Blitzeisen aus? Die vorbereiteten Gruben wurden mit „rohem“Wiesen- oder Sumpferz verfüllt. Der Schmelzraum solcher Öfen wurde mit Holzkohle gefüllt, die dann gründlich erhitzt wurde. Am Boden der Grube war ein Loch für die Luftzufuhr. Zunächst wurde mit Handbälgen geblasen, die später durch mechanische ersetzt wurden.
In den allerersten Schmieden wurde natürlicher Zug organisiert. Es wurde durch spezielle Löcher durchgeführt - Düsen, die sich an den Wänden des unteren Teils des Ofens befanden. Oft sorgten alte Metallurgen für die Luftzufuhr durch die Verwendung eines Designs, das es ermöglichte, die Wirkung einer Pfeife zu erzielen. Sie schufen einen hohen und gleichzeitig schmalen Innenraum. Sehr oft wurden solche Öfen am Fuße der Hügel gebaut. Diese Orte hatten den größten natürlichen Winddruck, der zur Erhöhung der Traktion genutzt wurde.
Als Ergebnis des laufenden Prozesses wurde Erz in Metall umgewandelt. Gleichzeitig floss der leere Felsen allmählich nach unten. Am Boden des Ofens bildeten sich Eisenkörner. Sie klebten aneinander und verwandelten sich in den sogenannten "Creep". Dies ist eine lockere schwammige Masse, die mit Schlacken imprägniert ist. Im Ofen war der Cracker weißglühend. In diesem Zustand nahmen sie es heraus und schmiedeten es schnell. Schlackenstücke fielen einfach ab. Als nächstes wurde das resultierende Material zu einem monolithischen Stück geschweißt. Das Ergebnis war auffälliges Eisen. Das Endprodukt hatte die Form eines Fladenbrots.
Was warZusammensetzung von Bloom-Eisen? Es war eine Legierung aus Fe und Kohlenstoff, die im Endprodukt sehr gering war (wenn wir den Prozentsatz berücksichtigen, dann nicht mehr als Hundertstel).
Allerdings war das aufgeblühte Eisen, das die Menschen im Rohofen erhielten, nicht sehr hart und h altbar. Deshalb versagten Produkte aus solchem Material schnell. Speere, Äxte und Messer waren verbogen und blieben nicht lange scharf.
Stahl
Bei der Herstellung von Eisen in Schmieden gab es neben seinen weichen Brocken auch solche, die eine höhere Härte aufwiesen. Dies waren Erzstücke, die während des Schmelzprozesses in engem Kontakt mit Holzkohle standen. Ein Mann bemerkte dieses Muster und begann, die Kontaktfläche mit Kohle bewusst zu vergrößern. Dadurch konnte das Eisen aufgekohlt werden. Das resultierende Metall begann, die Bedürfnisse der Handwerker und derjenigen zu erfüllen, die daraus hergestellte Produkte verwendeten.
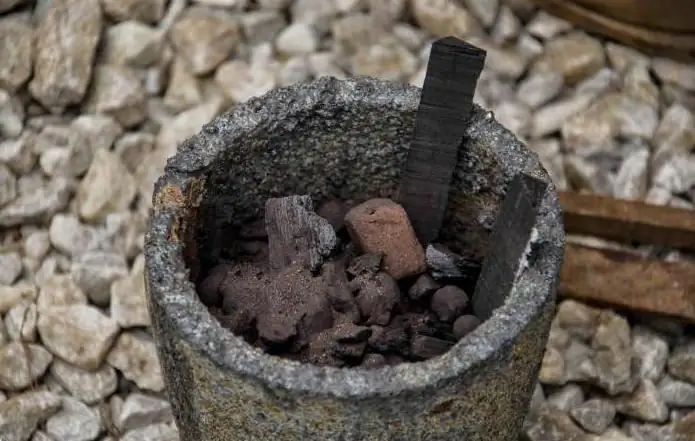
Dieses Material war Stahl. Es wird bis heute bei der Herstellung einer Vielzahl von Strukturen und Produkten verwendet. Stahl, der von alten Metallurgen geschmolzen wurde, ist Flash-Eisen, das bis zu 2 % Kohlenstoff enthält.
Es gab auch Weichstahl. Es war Flash-Eisen, das weniger als 0,25 % Kohlenstoff enthielt. Wenn wir die Geschichte der Metallurgie betrachten, dann war es Weichstahl, der in der Anfangsphase der Käseherstellung hergestellt wurde. Was ist ein anderer Name für Blitzeisen? Es gibt auch eine dritte Sorte. Wenn es mehr als 2 % Kohlenstoff enthält, dannes ist Gusseisen.
Erfindung des Hochofens
Die blühende Methode der Eisengewinnung mit Rohblutschmieden war stark wetterabhängig. Schließlich war es für eine solche Technologie wichtig, dass der Wind in das gefertigte Rohr blasen muss. Es war der Wunsch, den Launen des Wetters zu entfliehen, der eine Person dazu brachte, Pelze herzustellen. Dies waren die Geräte, die benötigt wurden, um das Feuer im Rohofen anzufachen.
Nach dem Aufkommen der Bälge wurden Schmieden zur Metallherstellung nicht mehr an Hängen gebaut. Die Menschen begannen, eine neue Art von Öfen zu benutzen, die "Wolfsgruben" genannt wurden. Es waren Bauwerke, von denen ein Teil im Boden lag und der zweite (Häuser) darüber in Form einer Struktur aus Steinen ragte, die durch Lehm zusammengeh alten wurden. Am Boden eines solchen Ofens befand sich ein Loch, in das ein Blasebalg eingeführt wurde, um das Feuer anzufachen. Die im Haus verlegte Kohle wurde verbrannt, danach war es möglich, den Cracker zu bekommen. Sie wurde durch das Loch herausgezogen, das nach dem Entfernen mehrerer Steine aus dem unteren Teil der Struktur entstanden war. Als nächstes wurde die Mauer restauriert und der Hochofen mit Erz und Kohle gefüllt, um von vorne anzufangen.

Die Blankeisenproduktion wurde ständig verbessert. Im Laufe der Zeit wurden die Häuser größer gebaut. Dies erforderte eine Steigerung der Produktivität der Mechs. Infolgedessen begann die Kohle schneller zu brennen und das Eisen mit Kohlenstoff zu sättigen.
Gusseisen
Wie heißt das kohlenstoffreiche Blitzeisen? Wie es waroben erwähnt, ist dies das heute so verbreitete Gusseisen. Sein Unterscheidungsmerkmal ist die Fähigkeit, bei relativ niedrigen Temperaturen zu schmelzen.
Ziegeleisen - Gusseisen in fester Form - es war unmöglich zu schmieden. Deshalb schenkten ihm die alten Metallurgen zunächst keine Beachtung. Durch einen einzigen Hammerschlag zersprang dieses Material einfach in Stücke. Insofern g alt Gusseisen wie auch Schlacke zunächst als Abfallprodukt. In England wurde dieses Metall sogar „Roheisen“genannt. Und erst im Laufe der Zeit wurde den Menschen klar, dass dieses Produkt in flüssiger Form in Formen gegossen werden kann, um verschiedene Produkte wie beispielsweise Kanonenkugeln zu erh alten. Dank dieser Entdeckung im 14.-15. Jahrhundert. in der Industrie mit dem Bau von Hochöfen zur Roheisenerzeugung. Die Höhe solcher Strukturen erreichte 3 Meter oder mehr. Mit ihrer Hilfe wurde Gießeisen für die Herstellung nicht nur von Kanonenkugeln, sondern auch der Kanonen selbst erschmolzen.
Entwicklung der Hochofenproduktion
Eine echte Revolution im Hüttengeschäft fand in den 80er Jahren des 18. Jahrhunderts statt. Damals entschied einer von Demidovs Angestellten, dass für mehr Effizienz beim Betrieb von Hochöfen Luft nicht durch eine, sondern durch zwei Düsen zugeführt werden sollte, die sich auf beiden Seiten des Herds befinden sollten. Allmählich wuchs die Anzahl solcher Düsen. Dadurch konnte der Blasprozess gleichmäßiger gest altet, der Herddurchmesser vergrößert und die Produktivität der Öfen gesteigert werden.
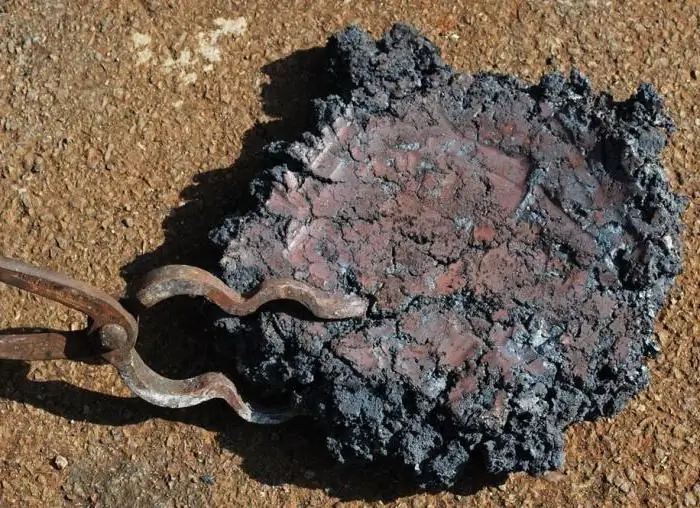
Die Entwicklung der Hochofenproduktion wurde auch durch den Ersatz von Holzkohle erleichtert,für die Wälder abgeholzt wurden, für Koks. 1829 wurde in Schottland im Werk Clayde zum ersten Mal heiße Luft in den Hochofen geblasen. Eine solche Innovation hat die Produktivität des Ofens erheblich gesteigert und den Brennstoffverbrauch gesenkt. Heutzutage wurde der Hochofenprozess verbessert, indem ein Teil des Kokses durch Erdgas ersetzt wurde, das noch kostengünstiger ist.
Bulat
Wie heißt das Blitzeisen, das einzigartige Eigenschaften hat, die bei der Herstellung von Waffen verwendet wurden? Wir kennen dieses Material als Damaststahl. Dieses Metall ist wie Damaststahl eine Legierung aus Eisen und Kohlenstoff. Im Gegensatz zu seinen anderen Arten ist es jedoch ein auffälliges Eisen mit guten Eigenschaften. Es ist belastbar und hart und auch in der Lage, der Klinge eine außergewöhnliche Schärfe zu verleihen.
Metallurgen vieler Länder versuchen seit mehr als einem Jahrhundert, das Geheimnis der Herstellung von Damaststahl zu lüften. Eine große Anzahl von Rezepten und Methoden wurde vorgeschlagen, die die Zugabe von Elfenbein, Edelsteinen, Gold und Silber zu Eisen beinh alteten. Das Geheimnis des Damaststahls wurde jedoch erst in der ersten Hälfte des 20. Jahrhunderts von dem bemerkenswerten russischen Metallurgen P. P. Anosov gelüftet. Sie nahmen blühendes Eisen, das mit Holzkohle in einen Ofen gelegt wurde, in dem ein offenes Feuer brannte. Das Metall schmolz, mit Kohlenstoff gesättigt. Damals wurde es mit kristalliner Dolomitschlacke bedeckt, teilweise unter Zugabe von reinstem Eisenzunder. Unter einer solchen Schicht wurde das Metall sehr intensiv von Silizium, Phosphor, Schwefel und Sauerstoff befreit. Das war jedoch noch nicht alles. Der resultierende Stahl musste so weit wie möglich gekühlt werdenlangsamer und ruhiger. Dadurch konnten zunächst große Kristalle mit verzweigter Struktur (Dendriten) gebildet werden. Diese Kühlung erfolgte direkt im Herd, der mit heißer Kohle gefüllt war. In der nächsten Phase wurde ein geschicktes Schmieden durchgeführt, bei dem die resultierende Struktur nicht zusammenbrechen sollte.
Die einzigartigen Eigenschaften von Damaststahl fanden später eine Erklärung in den Arbeiten eines anderen russischen Metallurgen D. K. Chernov. Er erklärte, dass Dendriten feuerfester, aber relativ weicher Stahl sind. Der Raum zwischen ihren "Zweigen" beim Erstarrungsprozess von Eisen ist mit mehr gesättigtem Kohlenstoff gefüllt. Das heißt, weicher Stahl ist von härterem Stahl umgeben. Dies erklärt die Eigenschaften von Damaststahl, die in seiner Viskosität und gleichzeitig hohen Festigkeit enth alten sind. Ein solcher Stahlhybrid behält während des Schmelzens seine Baumstruktur bei und dreht ihn nur von einer geraden Linie in eine Zickzacklinie. Die Besonderheit des resultierenden Musters hängt in hohem Maße von der Richtung der Schläge, der Stärke sowie dem Geschick des Schmieds ab.
Damaststahl
In der Antike war dieses Metall derselbe Damaststahl. Wenig später wurde Damaststahl jedoch als Material bezeichnet, das durch Schmiedeschweißen aus einer großen Anzahl von Drähten oder Bändern gewonnen wurde. Diese Elemente wurden aus Stahl hergestellt. Außerdem zeichnete sich jeder durch einen anderen Kohlenstoffgeh alt aus.
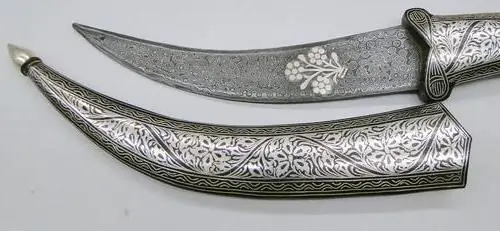
Die Kunst, ein solches Metall herzustellen, erreichte ihre größte Entwicklung im Mittel alter. Zum Beispiel in der Struktur der bekannten japanischen Klinge, die die Forscher fandenetwa 4 Millionen Stahlfäden von mikroskopischer Dicke. Diese Zusammensetzung machte die Herstellung von Waffen sehr mühsam.
Produktion unter modernen Bedingungen
Alte Metallurgen hinterließen eine Probe ihres Könnens nicht nur in Sachen Waffen. Das auffälligste Beispiel für reines Bloomery-Eisen ist die berühmte Säule in der Nähe der Hauptstadt Indiens. Archäologen bestimmten das Alter dieses Denkmals der metallurgischen Kunst. Es stellte sich heraus, dass die Säule vor weiteren 1,5 Tausend Jahren gebaut wurde. Aber das Überraschendste ist die Tatsache, dass es heute unmöglich ist, auch nur kleine Korrosionsspuren auf seiner Oberfläche zu entdecken. Das Material der Säule wurde einer sorgfältigen Prüfung unterzogen. Es stellte sich heraus, dass es sich um reines Flash-Eisen handelt, das nur 0,28 % Verunreinigungen enthält. Eine solche Entdeckung erstaunte sogar moderne Metallurgen.
Im Laufe der Zeit verlor auffälliges Eisen allmählich an Popularität. Das im offenen Herd oder Hochofen erschmolzene Metall begann sich der größten Nachfrage zu erfreuen. Bei der Anwendung dieser Verfahren wird jedoch ein Produkt mit unzureichender Reinheit erh alten. Aus diesem Grund hat die älteste Methode zur Herstellung dieses Materials kürzlich ihr zweites Leben erh alten, was die Herstellung von Metall mit den höchsten Qualitätsmerkmalen ermöglicht.
Wie heißt Blitzeisen heute? Es ist uns als Direktreduktionsmetall bekannt. Natürlich wird Bloomery Iron heute nicht mehr auf die gleiche Weise hergestellt wie in der Antike. Für seine Herstellung werden modernste Technologien eingesetzt. Sie ermöglichen die Herstellung von Metall, das praktisch keine hatfremde Verunreinigungen. In der Produktion werden Drehrohröfen eingesetzt. Solche Bauelemente werden zum Brennen verschiedener Schüttgüter bei hohen Temperaturen in der Chemie-, Zement- und vielen anderen Industrien eingesetzt.
Wie heißt Blitzeisen jetzt? Es gilt als rein und wird verwendet, um eine Methode zu erh alten, die sich im Wesentlichen nicht wesentlich von der unterscheidet, die in alten Zeiten existierte. Dennoch verwenden Metallurgen Eisenerz, das bei der Gewinnung des Endprodukts erhitzt wird. Allerdings werden Rohstoffe heute zunächst weiterverarbeitet. Es wird angereichert, wodurch eine Art Konzentrat entsteht.
Die moderne Industrie verwendet zwei Methoden. Beide ermöglichen es Ihnen, Blitzeisen aus Konzentrat zu gewinnen.
Die erste dieser Methoden basiert darauf, Rohstoffe mit festen Brennstoffen auf die erforderliche Temperatur zu bringen. Ein solcher Prozess ist dem der alten Metallurgen sehr ähnlich. Anstelle von Festbrennstoff kann auch Gas verwendet werden, das eine Kombination aus Wasserstoff und Kohlenmonoxid ist.
Was geht dem Erh alt dieses Materials voraus? Wie heißt Blitzeisen heute? Nach dem Erhitzen des Eisenerzkonzentrats verbleiben die Pellets im Ofen. Aus ihnen wird später reines Metall hergestellt.
Die zweite Methode zur Wiederherstellung von Eisen ist der ersten technologisch sehr ähnlich. Der einzige Unterschied besteht darin, dass Metallurgen reinen Wasserstoff als Brennstoff zum Erhitzen des Konzentrats verwenden. Mit dieser Methode wird Eisen viel schneller gewonnen. GenauDaher zeichnet es sich durch eine höhere Qualität aus, da bei der Wechselwirkung von Wasserstoff mit angereichertem Erz nur zwei Substanzen erh alten werden. Das erste davon ist reines Eisen und das zweite ist Wasser. Es ist davon auszugehen, dass dieses Verfahren in der modernen Metallurgie sehr beliebt ist. Heute wird es jedoch nur noch selten und in der Regel nur noch zur Herstellung von Eisenpulver verwendet. Dies erklärt sich aus der Tatsache, dass es ziemlich schwierig ist, reinen Wasserstoff zu erh alten, sowohl hinsichtlich der Lösung technischer Probleme als auch aufgrund wirtschaftlicher Schwierigkeiten. Auch die Aufbewahrung des erh altenen Brennstoffs ist eine schwierige Aufgabe.
Vor relativ kurzer Zeit haben Wissenschaftler eine weitere, dritte Methode zur Herstellung von reduziertem Eisen entwickelt. Es geht darum, Metall aus Erzkonzentrat zu gewinnen, ohne die Phase seiner Umwandlung in Pellets zu durchlaufen. Studien haben gezeigt, dass mit dieser Methode viel schneller reines Eisen hergestellt werden kann. Diese Methode wurde jedoch noch nicht in der Industrie umgesetzt, da sie erhebliche technologische Änderungen und eine Änderung der Ausrüstung von Metallurgieunternehmen erfordert.
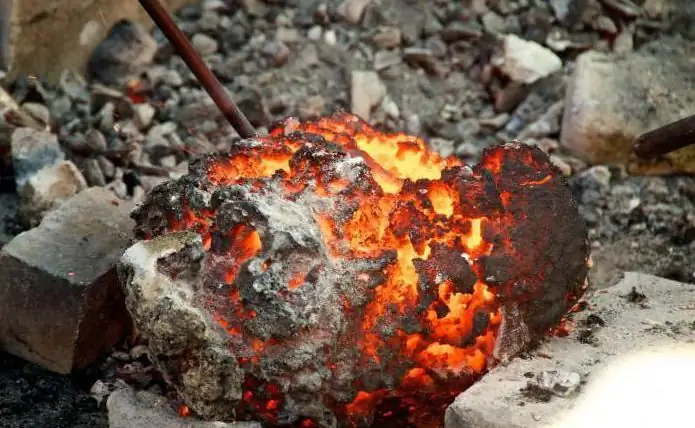
Wie heißt Blitzeisen heute? Dieses Material ist uns als Direktreduktionsmetall geläufig, manchmal wird es auch als Schwamm bezeichnet. Dies ist ein kostengünstiges, hochwertiges, umweltfreundliches Material, das keine Verunreinigungen von Phosphor und Schwefel aufweist. Bloomery Iron wird aufgrund seiner Eigenschaften in der Maschinenbauindustrie (Luftfahrt, Schiffbau und Instrumentierung) verwendet.
Fechral
Wie Sie sehen können, heute bei der VerwendungDie modernsten Technologien verwenden solche Materialien wie blühendes Eisen. Auch Fechral ist eine begehrte Legierung. Neben Eisen enthält es Bestandteile wie Chrom und Aluminium. Nickel ist ebenfalls in seiner Struktur vorhanden, jedoch nicht mehr als 0,6 %.
Fechral hat einen guten elektrischen Widerstand, eine hohe Härte, funktioniert hervorragend mit Keramiken mit hohem Aluminiumoxidgeh alt, neigt nicht zu Lochfraß und ist hitzebeständig in einer Atmosphäre, die Schwefel und seine Verbindungen, Wasserstoff und Kohlenstoff enthält. Das Vorhandensein von Eisen in der Legierung macht sie jedoch ziemlich spröde, was die Verarbeitung des Materials bei der Herstellung verschiedener Produkte erschwert.
Fechral wird zur Herstellung von Heizelementen für Labor- und Industrieöfen verwendet, deren maximale Betriebstemperatur 1400 Grad beträgt. Manchmal werden Teile aus dieser Legierung für andere Zwecke verwendet. Sie werden in Haush altsheizgeräten sowie in elektrischen Geräten mit thermischer Wirkung eingesetzt. Fechral wurde in großem Umfang bei der Herstellung von elektronischen Zigaretten verwendet. Auch eine Legierung aus Eisen, Aluminium und Chrom ist auf dem Gebiet der Herstellung von Widerstandselementen gefragt. Dies können z. B. Anfahr-Bremswiderstände von Elektrolokomotiven sein.
Fechral wird zur Herstellung von Draht, aber auch von Garnen und Bändern verwendet. Manchmal werden Kreise und Stäbe daraus gewonnen. Alle diese Produkte werden bei der Herstellung verschiedener Arten von Heizungen für Elektroöfen verwendet.