Die Qualitätskontrolle von Produkten ist ein wesentlicher Bestandteil des Property-Management-Systems. In jeder Produktionsphase gibt es spezifische Anforderungen an unterschiedliche Produktarten und damit an die verwendeten Materialien. Anfangs waren die Hauptanforderungen hauptsächlich Genauigkeit und Stärke, aber mit der Entwicklung der Industrie und der Kompliziertheit der hergestellten Ausrüstung hat sich die Anzahl der Eigenschaften, für die sie abgelehnt werden können, um ein Vielfaches erhöht.
Die zerstörungsfreie Überprüfung der Funktionsfähigkeit von Produkten ist durch die Verbesserung zerstörungsfreier Prüfverfahren möglich geworden. Arten und Methoden der Durchführung ermöglichen es Ihnen, eine Vielzahl von Parametern zu bewerten, ohne die Integrität des Produkts zu verletzen, und daher so genau wie möglich. Heutzutage hat kein einziger technologischer Prozess zur Herstellung verantwortungsbewusster Produkte ohne ein wohlgeformtes Kontrollsystem das Recht, in die Industrie eingeführt zu werden.
Das Konzept der zerstörungsfreien Prüfung
Dieser Prozess wird als eine Reihe von verstandensolche Tests, denen das Objekt direkt unterzogen wird, während es seine Leistung ohne Beschädigung des Materials beibehält. Alle heute existierenden Arten und Methoden der zerstörungsfreien Prüfung haben den Hauptzweck, die Arbeitssicherheit durch Überwachung des technischen Zustands von Anlagen, Gebäuden und Bauwerken zu gewährleisten. Sie werden nicht nur in der Phase der Produktion (Bau) durchgeführt, sondern auch für die rechtzeitige und qualitativ hochwertige Wartung und Reparatur.
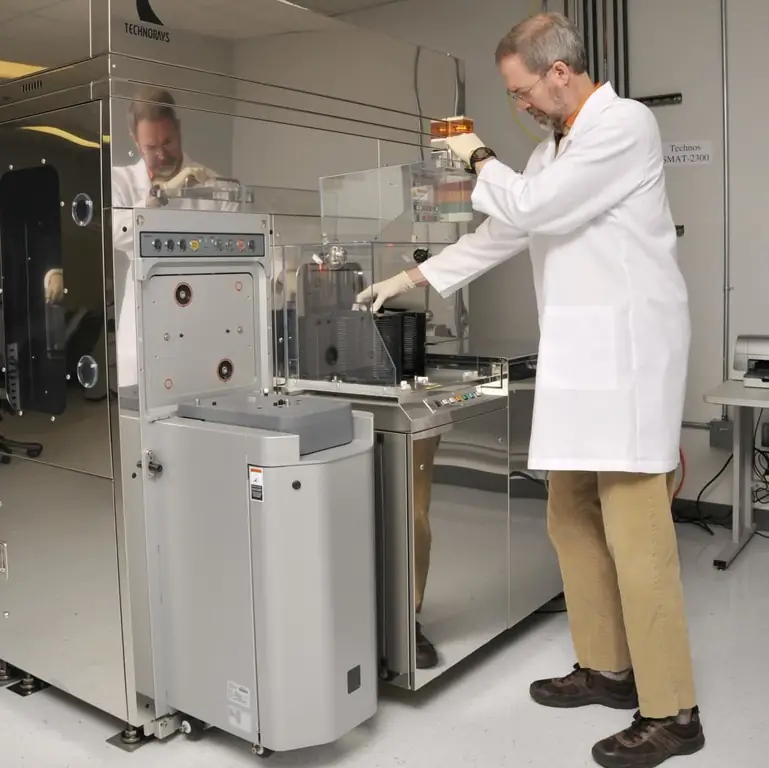
So können verschiedene Arten von zerstörungsfreien Prüfungen nach GOST die geometrischen Parameter von Produkten messen, die Qualität der Oberflächenbehandlung (z. B. Rauheit), die Struktur des Materials und seine chemische Zusammensetzung sowie das Vorhandensein bewerten von diversen Mängeln. Die Aktualität und Zuverlässigkeit der erh altenen Daten ermöglicht es Ihnen, den technologischen Prozess anzupassen und wettbewerbsfähige Produkte herzustellen sowie finanzielle Verluste zu vermeiden.
Prüfanforderungen
Damit die Ergebnisse aller Arten von zerstörungsfreien Prüfungen relevant und effektiv sind, müssen sie bestimmte Anforderungen erfüllen:
- die Möglichkeit der Implementierung in allen Phasen der Herstellung, während des Betriebs und der Reparatur von Produkten;
- Kontrolle sollte an der größtmöglichen Anzahl der gegebenen Parameter für eine bestimmte Produktion durchgeführt werden;
- Die für die Inspektion aufgewendete Zeit sollte angemessen mit anderen Schritten im Produktionsprozess korrelieren;
- die Zuverlässigkeit der Ergebnisse muss sehr hoch sein;
- vonMöglichkeiten zur technologischen Prozesskontrolle sollten mechanisiert und automatisiert werden;
- Zuverlässigkeit von Geräten und Ausrüstungen, die bei der zerstörungsfreien Prüfung verwendet werden, Arten und Bedingungen ihrer Verwendung sollten variiert werden;
- Einfachheit der Methoden, wirtschaftliche und technische Verfügbarkeit.
Bewerbungen
Die ganze Vielf alt der Arten und Methoden der zerstörungsfreien Prüfung nach GOST wird für folgende Zwecke eingesetzt:
- Erkennung von Fehlern in kritischen Teilen und Baugruppen (Kernreaktoren, Flugzeuge, Unterwasser- und Oberflächenwasserfahrzeuge, Raumfahrzeuge usw.);
- Defektoskopie von Geräten, die für den Langzeitbetrieb ausgelegt sind (Hafenanlagen, Brücken, Kräne, Kernkraftwerke und andere);
- Forschung nach Methoden der zerstörungsfreien Prüfung von Metallen, Arten ihrer Strukturen und möglicher Fehler in Produkten zur Verbesserung der Technologie;
- kontinuierliche Kontrolle über das Auftreten von Fehlern in Einheiten und Geräten der höchsten Verantwortung (z. B. Kessel von Kernkraftwerken).
Klassifizierung der Arten der zerstörungsfreien Prüfung
Basierend auf den Funktionsprinzipien von Geräten und physikalischen und chemischen Phänomenen werden alle Methoden in zehn Typen unterteilt:
- akustisch (insbesondere Ultraschall);
- vibroakustisch;
- mit eindringenden Substanzen (Kapillar- und Leckkontrolle);
- magnetisch (oder Magnetpartikel);
- optisch (visuell-optisch);
- Strahlung;
- Radiowelle;
- thermisch;
- elektrisch;
- Wirbelstrom (oder elektromagnetisch).
Nach GOST 56542 werden die oben aufgeführten Arten und Methoden der zerstörungsfreien Prüfung weiter nach folgenden Merkmalen unterteilt:
- Besonderheiten der Wechselwirkung von Stoffen oder physikalischen Feldern mit einem kontrollierten Objekt;
- primäre Parameter, die Informationen liefern;
- Hauptinformationen erh alten.
Akustische Methoden
Gemäß der Klassifizierung von Arten und Methoden der zerstörungsfreien Prüfung gemäß GOST R 56542-2015 basiert diese Art auf der Analyse elastischer Wellen, die angeregt werden und (oder) in einem kontrollierten Objekt entstehen. Wird ein Frequenzbereich größer als 20 kHz genutzt, darf anstelle von „akustisch“der Begriff „Ultraschall“verwendet werden.
Die akustische Art der zerstörungsfreien Prüfung wird in zwei große Gruppen unterteilt.
First - Methoden, die auf der Aussendung und dem Empfang von akustischen Wellen basieren. Zur Steuerung werden Wander- und Stehwellen oder Resonanzschwingungen des gesteuerten Objekts verwendet. Dazu gehören:
- Shadow-Methode. Das Vorhandensein eines Fehlers wird aufgrund der Dämpfung des empfangenen Signals oder der Verzögerung bei seiner Registrierung aufgrund der Rundung des Fehlers durch Ultraschallwellen erkannt.
- Echo-Methode. Das Vorhandensein eines Defekts wird durch die Ankunftszeit des vom Defekt und den Oberflächen des Objekts reflektierten Signals bestimmt, was es ermöglicht, den Ort des Defekts im Volumen des Materials zu bestimmen.
- Spiegel-Schatten-Methode. Es ist eine Variation der Schattenmethode, die Geräte aus verwendetEcho-Methode. Auch ein schwaches Signal ist ein Zeichen für einen Fehler.
- Impedanzmethode. Wenn das Produkt einen Fehler aufweist, nimmt die Impedanz eines bestimmten Bereichs seiner Oberfläche ab, als ob es weicher würde. Dies beeinflusst die Amplitude der Stabschwingungen, die mechanische Spannung an seinem Ende, die Phase der Schwingungen und die Verschiebung ihrer Frequenz.
- Resonanzmethode. Wichtig für die Messung der Schichtdicke. Der Fehler wird gefunden, indem der Sucher entlang der Oberfläche des Produkts bewegt wird, was auf eine Signalschwächung oder das Verschwinden der Resonanz hinweist.
- Methode der freien Schwingungen. Bei der Prüfung werden die Frequenzen der Eigenschwingungen der Probe analysiert, die durch Einwirkung auf diese entstehen.
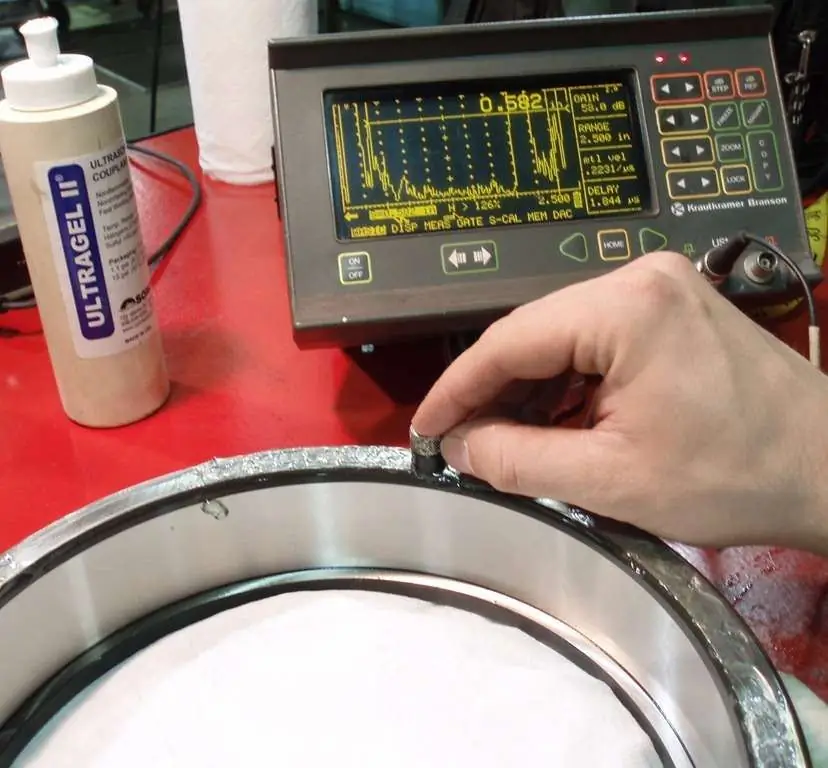
Die zweite Gruppe umfasst Methoden, die auf der Registrierung von Wellen beruhen, die in Produkten und Materialien entstehen:
- Akustische Emission. Es basiert auf der Registrierung von Wellen, die bei der Bildung und Entwicklung von Rissen auftreten. Gefährliche Defekte führen zu einer Erhöhung der Frequenz und Amplitude von Signalen in einem bestimmten Frequenzbereich.
- Noise-Vibration-Methode. Es besteht darin, das Frequenzspektrum des Mechanismus oder seiner Teile während des Betriebs zu beobachten.
Arten und Methoden der zerstörungsfreien Prüfung aus der oben angegebenen Klassifizierung werden für eine Vielzahl von Zwecken verwendet. Um die Parameter von gewalztem Metall mit geringer Dicke, Gummiprodukten, Glasfaser, Beton zu bestimmen, ist die Schattenmethode am besten geeignet. Sein wesentlicher Nachteil ist die Notwendigkeit, von zwei Seiten auf das Produkt zugreifen zu können. Mit Einwegzugriff aufdie Probe kann das Spiegelschatten- oder das Resonanzverfahren verwenden. Diese beiden Typen eignen sich gut für die zerstörungsfreie Prüfung von Schweißverbindungen sowie für die Schallemission. Das Impedanzverfahren sowie das Freischwingverfahren prüfen die Qualität von geklebten und gelöteten Produkten aus Glas, Metall und Kunststoff.
Kapillarmethoden
Nach der Klassifizierung von Arten und Methoden der zerstörungsfreien Prüfung gemäß GOST R 56542-2015 beziehen sich Kapillarmethoden auf die Untersuchung durch eindringende Substanzen.
Sie basieren auf dem Eindringen von Tropfen einer speziellen Flüssigkeit, die als Indikator bezeichnet wird, in die Defekthöhle. Das Verfahren beschränkt sich darauf, die Oberfläche des Teils zu reinigen und eine eindringende Flüssigkeit darauf aufzutragen. In diesem Fall werden die Hohlräume gefüllt, wonach die Flüssigkeit von der Oberfläche entfernt wird. Der Rest wird mit einem Entwickler erkannt, der ein Indikatormuster für die Fehlerstelle bildet.
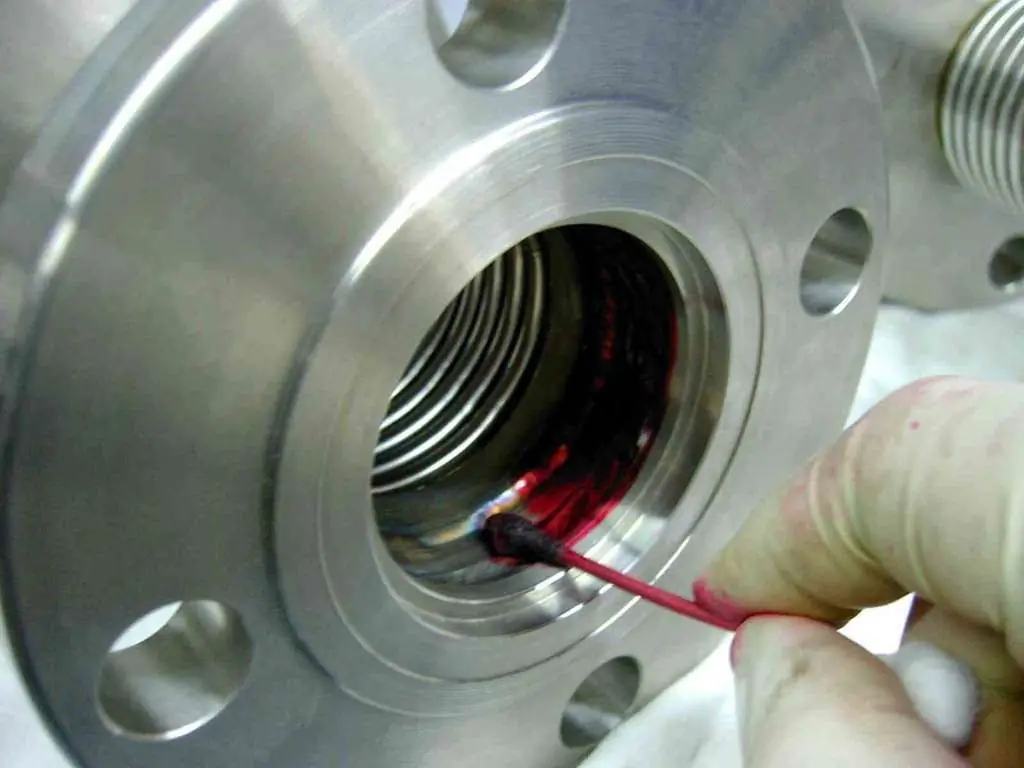
Die Sensitivität der kapillaren zerstörungsfreien Prüfung hängt weitgehend von der Wahl der Materialien zur Fehlersuche ab, was deren vorherige Überprüfung zwingend erforderlich macht. Die Indikatorfähigkeiten von Lösungen werden anhand einiger Standardlösungen überprüft. Der Weißgrad von Entwicklern wird durch Vergleich mit einer Schwerspatplatte (Weißgradstandard) überprüft.
Kapillarmethoden haben den Vorteil, dass sie unter Feld- und Laborbedingungen mit unterschiedlichen Umgebungstemperaturen eingesetzt werden können. Allerdings sind sie nur in der Lage, Oberflächendefekte bei nicht gefüllten Kavitäten zu detektieren. Kapillarmethoden sind anwendbar zErkennung von Fehlern in metallischen und nichtmetallischen Teilen verschiedener Formen.
Magnetische Verfahren
Sie basieren auf der Registrierung von Magnetfeldern, die über dem Defekt entstehen, oder auf der Bestimmung der magnetischen Eigenschaften der untersuchten Produkte. Mit magnetischen Methoden finden Sie Risse, Walzen und andere Defekte, wie z. B. die mechanischen Eigenschaften von ferromagnetischen Stählen und Gusseisen.
Die in GOST verfügbare Klassifizierung von zerstörungsfreien Arten und Methoden der Kontrolle sieht die Unterteilung von Magneten in die folgenden Unterarten vor:
- magnetografisch (Erfassung von Feldern erfolgt mit einem ferromagnetischen Film als Indikator);
- Magnetpartikel (Analyse von Magnetfeldern wird mit einem ferromagnetischen Pulver oder einer Magnetsuspension durchgeführt);
- Magnetoresistor (Erfassung von magnetischen Streufeldern erfolgt durch Magnetoresistoren);
- Induktionsart der magnetischen zerstörungsfreien Prüfung (die Größe oder Phase der induzierten EMF wird überwacht);
- ponderomotive (die Kraft des Magnetrückrufs von einem kontrollierten Objekt wird aufgezeichnet);
- ferroprobe (basierend auf der Messung der Magnetfeldstärke mit Fluxgates);
- Hall-Effekt-Verfahren (Magnetfelder werden von Hall-Sensoren erfasst).
Optische Methoden
Die Art der zerstörungsfreien Prüfung, die auf der Einwirkung von Lichtstrahlung auf ein Objekt mit der Registrierung der Ergebnisse dieser Aktion basiert, wird als optisch bezeichnet. Herkömmlicherweise gibt es drei Gruppen von Methoden:
Visuell (wie auch das visuell-optische Verfahren) basiert auf den persönlichen Eigenschaften des Operateurs (Laborassistent): Erfahrung, Geschicklichkeit, Sehvermögen. Es ist sehr zugänglich und einfach durchzuführen, was seine Allgegenwärtigkeit erklärt. Die visuelle Kontrolle erfolgt ohne optische Mittel. Es ist effektiv bei großen Objekten, um grobe Fehler, Verletzungen der Geometrie und Abmessungen zu erkennen. Die visuell-optische Analyse erfolgt mit optischen Hilfsmitteln wie Lupe oder Mikroskop. Es ist weniger produktiv, daher wird es normalerweise mit visuellen kombiniert
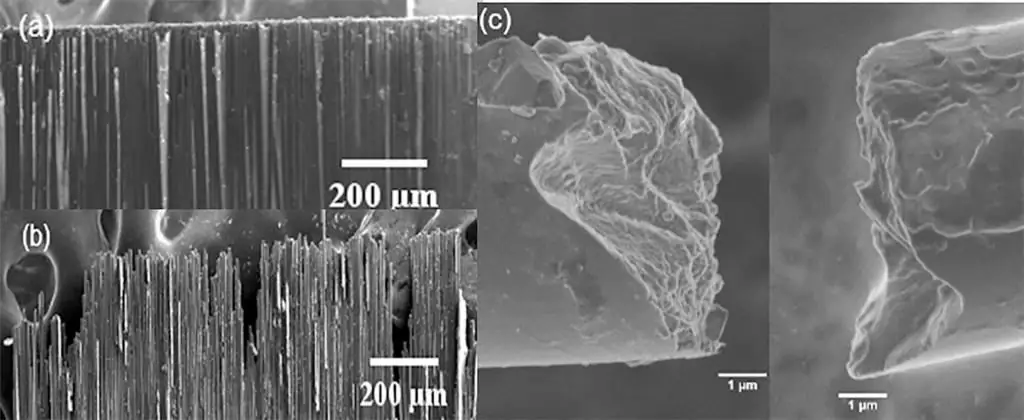
- Photometrische, densitometrische, Spektral- und Fernsehverfahren basieren auf instrumentellen Messungen und zeichnen sich durch weniger Subjektivität aus. Diese Arten der optischen zerstörungsfreien Prüfung sind unentbehrlich für die Messung geometrischer Abmessungen, Oberflächenbereiche, die Kontrolle des Dämpfungskoeffizienten, die Bewertung der Transmission oder des Reflexionsvermögens und die Fehlererkennung.
- Interferenz-, Beugungs-, Phasenkontrast-, Refraktometrie-, Nephelometrie-, Polarisations-, Stroboskop-, Holographieverfahren basieren auf den Welleneigenschaften des Lichts. Mit ihrer Hilfe können Sie Produkte aus Materialien kontrollieren, die für Lichteinstrahlung transparent oder durchscheinend sind.
Bestrahlungsverfahren
Basierend auf der Wirkung ionisierender elektromagnetischer Strahlung auf ein Objekt, gefolgt von der Registrierung der Parameter dieser Aktion und der Zusammenfassung der Kontrollergebnisse. Für die Strahlungsart der zerstörungsfreien Prüfung werden verschiedene Strahlungen verwendet, die es ermöglichen, ihre Quanten durch folgende physikalische Größen zu beschreiben: Frequenz, Wellenlänge bzwEnergie.
Beim Durchgang durch das Produkt werden Röntgen- oder Gammastrahlung sowie Neutrinoflüsse in Bereichen mit und ohne Defekte unterschiedlich stark abgeschwächt. Sie ermöglichen es Ihnen, das interne Vorhandensein von Fehlern zu beurteilen. Sie werden erfolgreich zur Prüfung von Schweiß- und Lötnähten, Walzprodukten eingesetzt.
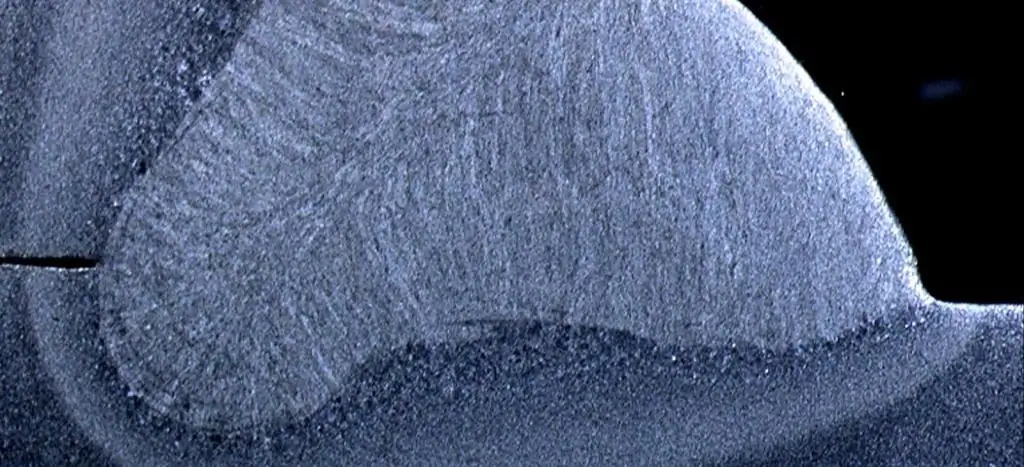
Strahlungsarten der zerstörungsfreien Prüfung bergen eine biologische Gefahr, da sie im Verborgenen wirken. Dies erfordert die Einh altung der organisatorischen und hygienischen Normen des Arbeitsschutzes und der Sicherheitsvorschriften.
Thermische Verfahren
Ein wichtiger Parameter ist die Registrierung von Änderungen, die in den thermischen oder Temperaturfeldern der analysierten Probe auftreten. Zur Kontrolle werden die Temperatur und Unterschiede in den thermischen Eigenschaften des Objekts gemessen.
NDT thermische Ansicht kann passiv oder aktiv sein. Im ersten Fall werden die Proben nicht von externen Wärmequellen beeinflusst und das Temperaturfeld wird am Antrieb gemessen. Ein Anstieg oder Abfall der Temperatur an einigen Stellen kann auf das Vorhandensein von Mängeln hinweisen, z. B. Risse in Motoren. Bei aktiver Temperaturregelung werden Materialien oder Produkte erwärmt oder gekühlt und die Temperatur von ihren beiden gegenüberliegenden Seiten gemessen.
Um genaue und objektive Daten zu erh alten, werden die folgenden primären Messwandler der Wärmestrahlung verwendet: Thermometer, Thermoelemente, thermische Widerstände, Halbleiterbauelemente, elektronische Vakuumbauelemente, pyroelektrische Elemente. Oft werden Indikatoren für thermische Felder verwendet, die sindPlatten, Pasten, Filme aus wärmeempfindlichen Stoffen, die sich bei Erreichen bestimmter Temperaturen verändern. So werden schmelzende Wärmeindikatoren, farbwechselnde Wärmeindikatoren und Phosphore isoliert.
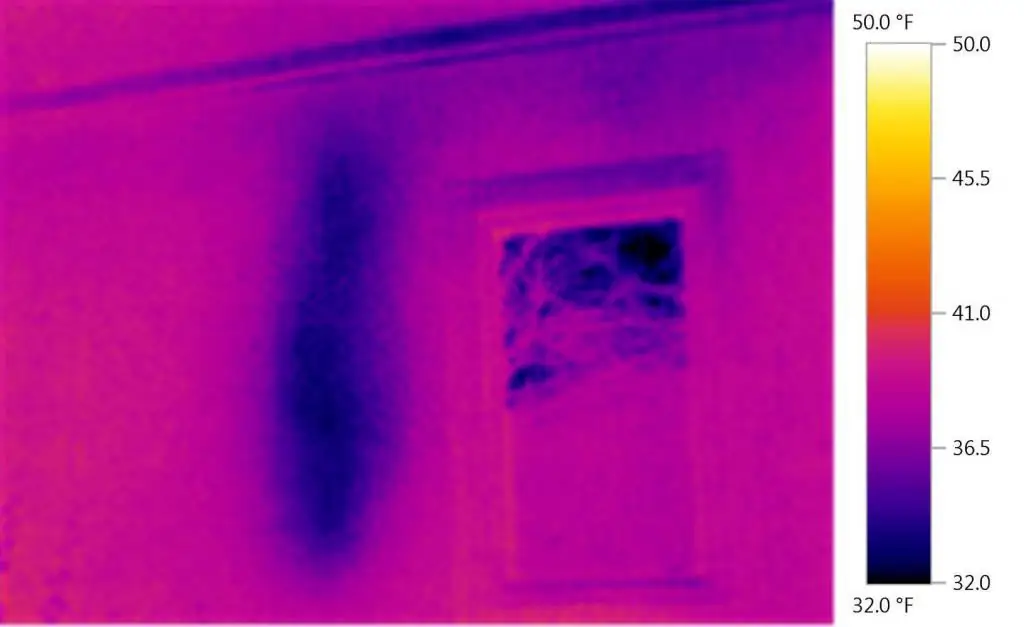
Thermische Verfahren ermöglichen durch den Einsatz spezieller Geräte die berührungslose Messung der physikalischen und geometrischen Parameter von Objekten aus größeren Entfernungen. Sie ermöglichen auch die Erkennung chemischer und physikalischer Verschmutzungen, Rauheiten und Beschichtungen auf ihren Oberflächen, basierend auf den Werten des thermischen Emissionsvermögens.
Lecksuchverfahren
Nach der Hauptklassifizierung der Arten der zerstörungsfreien Prüfung bezieht sich diese Methode auf die Prüfung von Proben mit eindringenden Flüssigkeiten. Die Lecksuche deckt Mängel an Produkten und Bauwerken auf, indem Prüfsubstanzen durch sie hindurchdringen. Wird oft als Leckkontrolle bezeichnet.
Flüssigkeiten, einige Gase, Flüssigkeitsdämpfe können als Prüfsubstanzen dienen. Gemäß diesem Parameter werden Lecksuchkontrollmethoden in Flüssigkeiten und Gase unterteilt. Gase bieten eine höhere Empfindlichkeit, was bedeutet, dass sie häufiger verwendet werden. Auch die Empfindlichkeit des Verfahrens wird durch die verwendete Ausrüstung beeinflußt. Vakuumtechnik ist in diesem Fall die beste Option.
Zur Lecksuche werden spezielle Geräte benötigt, sogenannte Lecksucher, aber in manchen Fällen sind auch gerätelose Methoden zur Lecksuche geeignet. Zur Kontrolle dieser Methode werden folgende Lecksucher verwendet:
- Massenspektrometrie - vom Größten geprägtSensitivität und Vielseitigkeit ermöglicht es Ihnen, Produkte unterschiedlicher Abmessungen zu untersuchen. All dies erklärt seine breite Anwendung. Aber das Massenspektrometer ist ein sehr komplexes und sperriges Instrument, für dessen Betrieb ein Vakuum erforderlich ist.
- Halogen, dessen Wirkung auf einem starken Anstieg der Emission von Alkalimetallkationen beruht, wenn Halogene in der Testsubstanz auftreten.
- Blase - basiert auf der Erkennung von Testgasblasen, die während der Gasdruckprüfung eines kontrollierten Objekts aus einem Leck freigesetzt werden, wobei Flüssigkeit auf seine Oberfläche aufgetragen oder in einen Tank eingetaucht wird. Dies ist eine ziemlich einfache Methode, die keine komplexen Instrumente und Spezialgase erfordert, aber eine hohe Empfindlichkeit bietet.
- Manometrie - ermöglicht Ihnen, die Dichtheit des Testobjekts mit Manometern zu bewerten, die den Druck von Testgasen messen.
Elektrische Methoden
Diese Art der zerstörungsfreien Prüfung nach GOST R 56542-2015 basiert auf der Analyse der Parameter des elektrischen Feldes (oder Stroms), das auf das kontrollierte Objekt einwirkt oder durch äußere Einflüsse im Objekt entsteht.
In diesem Fall informative Parameter - elektrische Kapazität oder Potential. Zur Ansteuerung von Dielektrika oder Halbleitern wird das kapazitive Verfahren eingesetzt. Es ermöglicht Ihnen, die chemische Zusammensetzung von Kunststoffen und Halbleitern zu analysieren, Ungänzen darin zu erkennen und den Feuchtigkeitsgeh alt von Schüttgütern zu bewerten.
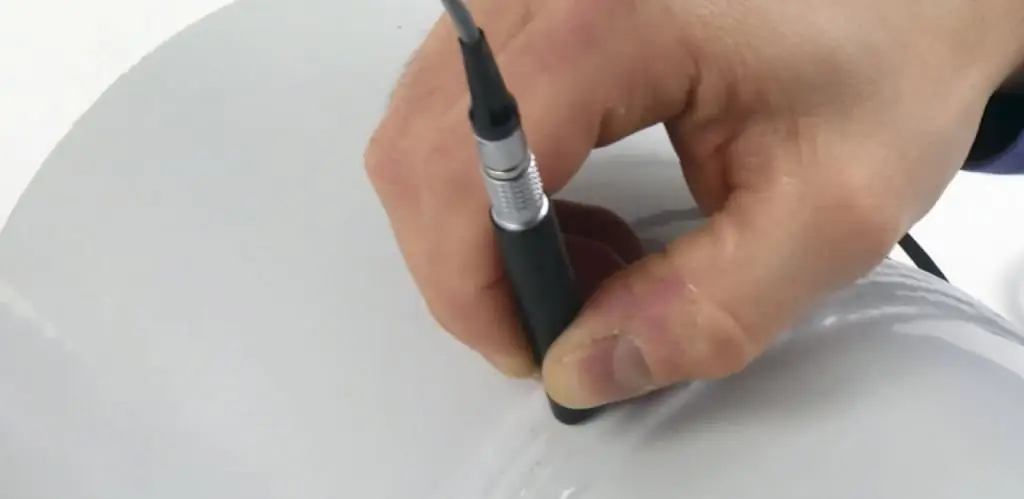
Die Kontrolle der Leiter erfolgt nach der Methode des elektrischen Potentials. In diesem Fall ist die Dicke der leitfähigen Schicht das Vorhandensein von Diskontinuitätenin der Nähe der Oberfläche des Leiters wird durch Messen des Potentialabfalls in einem bestimmten Bereich kontrolliert.
Wirbelstromverfahren
Hat einen anderen Namen - die Wirbelstrommethode. Es basiert auf Änderungen in der Wirkung des elektromagnetischen Feldes einer Spule mit einem Feld von Wirbelströmen, die von dieser Spule in einem gesteuerten Objekt induziert werden. Geeignet zum Erkennen von Oberflächenfehlern an magnetischen und nichtmagnetischen Teilen und Halbzeugen. Ermöglicht es Ihnen auch, Risse an Produkten mit verschiedenen Konfigurationen zu finden.
Der Wert des Wirbelstromverfahrens liegt darin, dass weder Feuchtigkeit noch Druck noch Umweltverschmutzung noch radioaktive Strahlung und selbst die Verunreinigung des Objekts mit nichtleitenden Stoffen praktisch keinen Einfluss auf das Messsignal haben. Seine Anwendungsgebiete sind wie folgt:
- Überprüfung der Längenmaße von Produkten (z. B. Stangendurchmesser, Rohre, Blechdicke, Karosseriewanddicke).
- Messung der Dicke aufgetragener Beschichtungen (Bereich von Mikrometer bis zu mehreren zehn Millimetern).
- Bestimmung von Abweichungen in der Zusammensetzung und Struktur von Metallen und Legierungen.
- Bestimmung mechanischer Spannungswerte.
Vor- und Nachteile zerstörungsfreier Verfahren
Trotz der Tatsache, dass beide Arten der Prüfung, zerstörend und zerstörungsfrei, ihre Vor- und Nachteile haben, hat letztere unter modernen Produktionsbedingungen eine Reihe von Vorteilen:
- Produkte, die unter Arbeitsbedingungen verwendet werden, werden sofort getestet.
- Die Vermessung kann an jedem Teil oder jeder Unterbaugruppe durchgeführt werden, die für den Einsatz in der realen Welt bestimmt ist, aberwenn es wirtschaftlich gerechtfertigt ist. Oft ist dies sogar möglich, wenn die Charge durch große Unterschiede zwischen den Teilen gekennzeichnet ist.
- Sie können den ganzen Teil oder nur die gefährlichsten Teile davon testen. Abhängig von der Bequemlichkeit des Dirigierens oder den technologischen Bedingungen können sie gleichzeitig oder nacheinander durchgeführt werden.
- Dasselbe Objekt kann mit vielen zerstörungsfreien Prüfverfahren getestet werden, von denen jedes empfindlich auf bestimmte Eigenschaften oder Teile des Teils reagiert.
- Zerstörungsfreie Methoden können unter Betriebsbedingungen auf das Gerät angewendet werden, und es besteht keine Notwendigkeit, seinen Betrieb einzustellen. Sie verursachen keine Störungen und Veränderungen der Eigenschaften der Teile.
- Durch Testen können Sie dieselben Teile nach einer beliebigen Zeit erneut überprüfen. Dadurch ist es möglich, einen Zusammenhang zwischen den Betriebsarten und den daraus resultierenden Schäden und deren Ausmaß herzustellen.
- Zerstörungsfreie Prüfung ermöglicht, dass Teile aus teuren Materialien nicht beschädigt werden.
- Prüfungen werden in der Regel ohne Probenvorbehandlung durchgeführt. Viele Analysegeräte sind tragbar und schnell und oft automatisiert.
- Die Kosten der zerstörungsfreien Prüfung sind niedriger als die der zerstörenden Verfahren.
- Die meisten Methoden sind schnell und benötigen weniger Arbeitsstunden. Solche Methoden sollten verwendet werden, um die Qualität aller Details zu bestimmen, wenn ihre Kosten geringer oder vergleichbar mit den Kosten für die Durchführung einer destruktiven Untersuchung sind.nur ein kleiner Prozentsatz der Teile in der gesamten Charge.
Zerstörungsfreie Prüfverfahren haben nicht so viele Nachteile:
- In der Regel werden indirekte Eigenschaften analysiert, die keinen direkten Zusammenhang mit den Werten im Betrieb haben. Für die Zuverlässigkeit der Ergebnisse wird ein indirekter Zusammenhang zwischen den erh altenen Daten und der Betriebssicherheit festgestellt.
- Die meisten Tests zeigen nicht die Lebensdauer des Objekts an, sondern können nur die Zerstörungsprozesse verfolgen.
- Um die Ergebnisse der analytischen Arbeit zu entschlüsseln und zu interpretieren, müssen die gleichen Untersuchungen auch an speziellen Proben und unter speziellen Bedingungen durchgeführt werden. Und wenn die relevante Verbindung zwischen diesen Tests nicht offensichtlich und bewiesen ist, dann können Beobachter dem nicht zustimmen.
Wir haben die Arten der zerstörungsfreien Prüfung, ihre Merkmale und Nachteile analysiert.