Um die Leistungseigenschaften von Produkten zu bewerten und die physikalischen und mechanischen Eigenschaften von Materialien zu bestimmen, werden verschiedene Anweisungen, GOSTs und andere regulatorische und beratende Dokumente verwendet. Empfehlenswert sind auch Methoden zur Prüfung der Zerstörung einer ganzen Reihe von Produkten oder Proben der gleichen Materialart. Dies ist keine sehr wirtschaftliche Methode, aber effektiv.
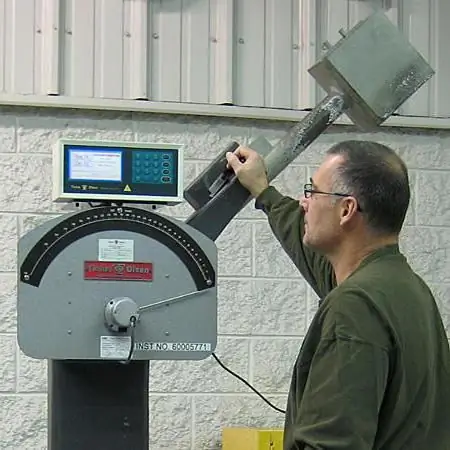
Definition von Merkmalen
Die Hauptmerkmale der mechanischen Eigenschaften von Materialien sind wie folgt.
1. Zugfestigkeit oder Zugfestigkeit - jene Spannungskraft, die bei der höchsten Belastung vor der Zerstörung der Probe feststeht. Die mechanischen Eigenschaften Festigkeit und Plastizität von Werkstoffen beschreiben die Eigenschaften von Festkörpern, irreversiblen Formänderungen und Zerstörungen unter Einwirkung äußerer Belastungen zu widerstehen.
2. Die bedingte Streckgrenze ist die Spannung, wenn die Restdehnung 0,2 % der Probenlänge erreicht. Dasdie geringste Spannung, während sich die Probe ohne merkliche Spannungserhöhung weiter verformt.
3. Als Grenze der Dauerfestigkeit wird die größte Belastung bezeichnet, die bei einer gegebenen Temperatur für eine bestimmte Zeit zur Zerstörung der Probe führt. Die Bestimmung der mechanischen Eigenschaften von Werkstoffen konzentriert sich auf die letzten Einheiten der Dauerfestigkeit - die Zerstörung erfolgt bei 7.000 Grad Celsius in 100 Stunden.
4. Die bedingte Kriechgrenze ist die Spannung, die bei einer bestimmten Temperatur für eine bestimmte Zeit in der Probe eine bestimmte Dehnung sowie die Kriechgeschwindigkeit bewirkt. Die Grenze ist die Verformung des Metalls für 100 Stunden bei 7.000 Grad Celsius um 0,2 %. Kriechen ist eine bestimmte Verformungsgeschwindigkeit von Metallen unter konstanter Belastung und hoher Temperatur über einen langen Zeitraum. Hitzebeständigkeit ist die Widerstandsfähigkeit eines Materials gegen Bruch und Kriechen.
5. Die Ermüdungsgrenze ist der höchste Wert der Zyklusbeanspruchung, wenn kein Ermüdungsbruch auftritt. Die Anzahl der Belastungszyklen kann vorgegeben oder beliebig sein, je nachdem wie die mechanische Werkstoffprüfung geplant ist. Zu den mechanischen Eigenschaften gehören Ermüdung und Beständigkeit des Materials. Unter Einwirkung von Lasten im Kreislauf häufen sich Schäden, es bilden sich Risse, die zur Zerstörung führen. Das ist Müdigkeit. Und die Eigenschaft der Ermüdungsbeständigkeit ist Ausdauer.
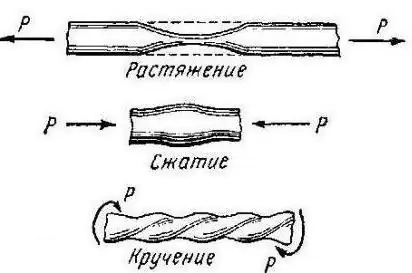
Dehnung und Schrumpfung
In der Technik verwendete MaterialienDie Praxis wird in zwei Gruppen eingeteilt. Der erste ist plastisch, für dessen Zerstörung erhebliche Restverformungen auftreten müssen, der zweite ist spröde und bricht bei sehr kleinen Verformungen zusammen. Natürlich ist eine solche Einteilung sehr willkürlich, da sich jeder Werkstoff je nach den geschaffenen Bedingungen sowohl spröde als auch duktil verh alten kann. Sie hängt von der Art des Spannungszustands, der Temperatur, der Dehnungsrate und anderen Faktoren ab.
Die mechanischen Eigenschaften von Materialien unter Spannung und Druck sind sowohl für duktile als auch für spröde beredt. Weichstahl wird beispielsweise unter Spannung getestet, während Gusseisen unter Druck getestet wird. Gusseisen ist spröde, Stahl ist duktil. Spröde Materialien haben eine höhere Druckfestigkeit, während die Zugverformung schlechter ist. Kunststoffe haben bei Druck und Zug annähernd die gleichen mechanischen Eigenschaften wie Materialien. Ihre Schwelle wird jedoch immer noch durch Dehnung bestimmt. Mit diesen Methoden können die mechanischen Eigenschaften von Materialien genauer bestimmt werden. Das Zug- und Druckdiagramm ist in den Illustrationen zu diesem Artikel dargestellt.
Fragilität und Plastizität
Was ist Plastizität und Fragilität? Die erste ist die Fähigkeit, nicht zusammenzubrechen und Restverformungen in großen Mengen zu erh alten. Diese Eigenschaft ist entscheidend für die wichtigsten technologischen Operationen. Biegen, Ziehen, Ziehen, Stanzen und viele andere Operationen hängen von den Eigenschaften der Plastizität ab. Zu duktilen Materialien gehören geglühtes Kupfer, Messing, Aluminium, Weichstahl, Gold und dergleichen. Viel weniger duktile Bronzeund dural. Fast alle legierten Stähle sind sehr schwach duktil.
Die Festigkeitseigenschaften von Kunststoffmaterialien werden mit der Streckgrenze verglichen, auf die weiter unten eingegangen wird. Die Eigenschaften Sprödigkeit und Plastizität werden stark von Temperatur und Belastungsgeschwindigkeit beeinflusst. Schnelle Spannung macht das Material spröde, während langsame Spannung es duktil macht. Beispielsweise ist Glas ein sprödes Material, das jedoch bei normaler Temperatur einer Langzeitbelastung standh alten kann, dh es zeigt die Eigenschaften der Plastizität. Und Baustahl ist duktil, aber unter Stoßbelastung erscheint er als sprödes Material.
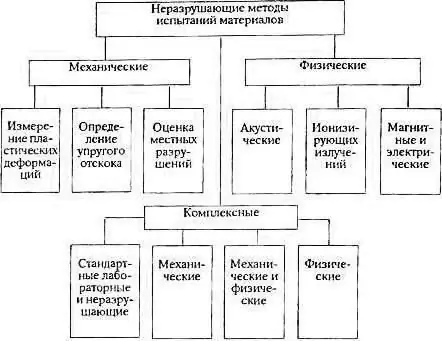
Variationsmethode
Physiko-mechanische Eigenschaften von Materialien werden durch die Anregung von Längs-, Biege-, Torsions- und anderen, noch komplexeren Arten von Schwingungen und je nach Größe der Proben, Formen, Empfänger- und Erregertypen, Methoden bestimmt von Befestigungen und Schemata zum Aufbringen dynamischer Lasten. Auch großformatige Produkte unterliegen der Prüfung nach diesem Verfahren, wenn die Art der Aufbringung in den Verfahren der Belastungsaufbringung, Schwingungsanregung und deren Erfassung wesentlich verändert wird. Die gleiche Methode wird verwendet, um die mechanischen Eigenschaften von Materialien zu bestimmen, wenn es notwendig ist, die Steifigkeit von großen Strukturen zu bewerten. Dieses Verfahren wird jedoch nicht zur lokalen Bestimmung von Materialeigenschaften in einem Produkt verwendet. Die praktische Anwendung der Technik ist nur möglich, wenn die geometrischen Abmessungen und die Dichte bekannt sind, wenn es möglich ist, das Produkt auf Trägern zu befestigen, und auf derProdukt - Konverter, bestimmte Temperaturbedingungen sind erforderlich usw.
Zum Beispiel, wenn sich die Temperaturregime ändern, tritt die eine oder andere Änderung auf, die mechanischen Eigenschaften von Materialien werden beim Erhitzen unterschiedlich. Fast alle Körper dehnen sich unter diesen Bedingungen aus, was sich auf ihre Struktur auswirkt. Jeder Körper hat bestimmte mechanische Eigenschaften der Materialien, aus denen er besteht. Wenn sich diese Eigenschaften nicht in alle Richtungen ändern und gleich bleiben, wird ein solcher Körper als isotrop bezeichnet. Wenn sich die physikalischen und mechanischen Eigenschaften von Materialien ändern - anisotrop. Letzteres ist ein charakteristisches Merkmal fast aller Materialien, nur in unterschiedlichem Maße. Aber es gibt zum Beispiel Stähle, bei denen die Anisotropie sehr unbedeutend ist. Es ist am ausgeprägtesten in natürlichen Materialien wie Holz. Unter Produktionsbedingungen werden die mechanischen Eigenschaften von Materialien durch Qualitätskontrolle bestimmt, bei der verschiedene GOSTs verwendet werden. Eine Schätzung der Heterogenität wird aus der statistischen Verarbeitung erh alten, wenn die Testergebnisse zusammengefasst werden. Muster sollten zahlreich sein und aus einem bestimmten Design geschnitten werden. Diese Methode zur Erlangung technologischer Eigenschaften gilt als recht mühsam.
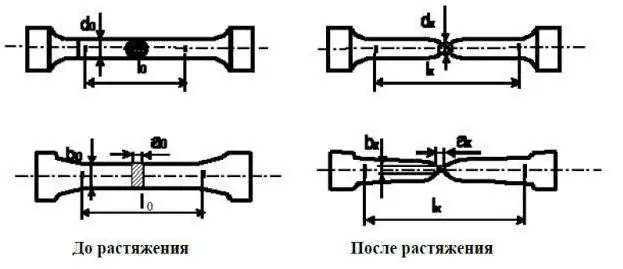
Akustische Methode
Es gibt viele akustische Methoden zur Bestimmung der mechanischen Eigenschaften von Materialien und ihrer Eigenschaften, die sich alle in der Art der Einkopplung, Aufnahme und Registrierung von Schwingungen im Sinus- und Pulsmodus unterscheiden. Akustische Verfahren werden beispielsweise bei der Untersuchung von Baumaterialien, ihrer Dicke und ihres Spannungszustands bei der Fehlersuche eingesetzt. Auch die mechanischen Eigenschaften von Strukturwerkstoffen werden mit akustischen Methoden bestimmt. Es werden bereits zahlreiche verschiedene elektroakustische Geräte entwickelt und in Serie hergestellt, die es ermöglichen, elastische Wellen und ihre Ausbreitungsparameter sowohl im sinusförmigen als auch im gepulsten Modus aufzuzeichnen. Auf ihrer Grundlage werden die mechanischen Eigenschaften der Festigkeit von Materialien bestimmt. Wenn elastische Schwingungen geringer Intensität verwendet werden, wird diese Methode absolut sicher.
Der Nachteil der akustischen Methode ist die Notwendigkeit eines akustischen Kontakts, der nicht immer möglich ist. Daher sind diese Arbeiten nicht sehr produktiv, wenn es dringend erforderlich ist, die mechanischen Eigenschaften der Materialfestigkeit zu erh alten. Das Ergebnis wird stark vom Zustand der Oberfläche, den geometrischen Formen und Abmessungen des untersuchten Produkts sowie der Umgebung beeinflusst, in der die Tests durchgeführt werden. Um diese Schwierigkeiten zu überwinden, muss ein bestimmtes Problem durch eine genau definierte akustische Methode gelöst werden, oder im Gegenteil, es sollten mehrere davon gleichzeitig verwendet werden, es hängt von der spezifischen Situation ab. Beispielsweise eignet sich Glasfaser gut für eine solche Untersuchung, da die Ausbreitungsgeschwindigkeit elastischer Wellen gut ist und daher eine durchgehende Sondierung weit verbreitet ist, wenn sich Empfänger und Sender auf gegenüberliegenden Oberflächen der Probe befinden.
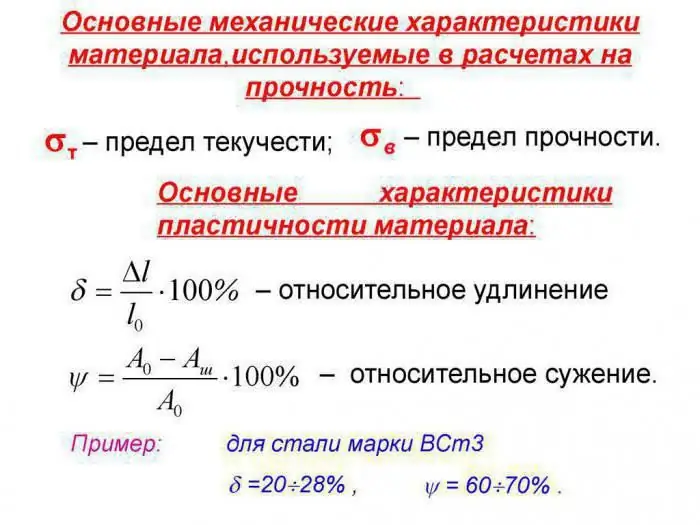
Defektoskopie
Defektoskopische Methoden werden zur Qualitätskontrolle von Materialien in verschiedenen Branchen eingesetzt. Es gibt zerstörungsfreie und destruktive Verfahren. Nicht-destruktiv umfasst Folgendes.
1. Die magnetische Fehlersuche dient der Bestimmung von Oberflächenrissen und Durchdringungsfehlern. Bereiche mit solchen Defekten sind durch Streufelder gekennzeichnet. Sie können sie mit speziellen Geräten erkennen oder einfach eine Schicht Magnetpulver auf die gesamte Oberfläche auftragen. An Stellen mit Defekten verändert sich die Lage des Pulvers auch beim Auftragen.
2. Die Defektoskopie wird auch mit Hilfe von Ultraschall durchgeführt. Der gerichtete Strahl wird unterschiedlich reflektiert (gestreut), auch wenn es tief im Inneren der Probe Ungänzen gibt.
3. Defekte im Material werden durch die Strahlungsforschungsmethode gut gezeigt, basierend auf dem Unterschied in der Absorption von Strahlung durch ein Medium unterschiedlicher Dichte. Gammafehlererkennung und Röntgen werden verwendet.
4. Chemische Fehlererkennung. Wenn die Oberfläche mit einer schwachen Lösung aus Salpetersäure, Salzsäure oder einer Mischung davon (Königswasser) geätzt wird, erscheint an Stellen mit Defekten ein Netzwerk in Form von schwarzen Streifen. Sie können eine Methode anwenden, bei der Schwefelabdrücke entfernt werden. An Stellen, wo das Material inhomogen ist, sollte Schwefel seine Farbe ändern.
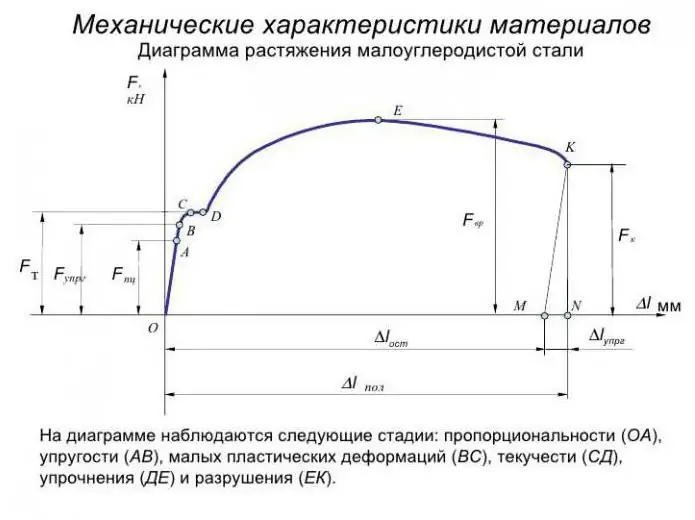
Destruktive Methoden
Destruktive Methoden sind hier bereits teilweise abgebaut. Proben werden auf Biegung, Druck, Zug getestet, dh es werden statische Zerstörungsmethoden verwendet. Wenn das Produktwerden mit variablen zyklischen Belastungen auf Schlagbiegung geprüft - dynamische Eigenschaften werden ermittelt. Makroskopische Methoden zeichnen ein allgemeines Bild der Struktur des Materials und in großen Volumina. Für eine solche Untersuchung werden speziell polierte Proben benötigt, die einer Ätzung unterzogen werden. So ist es möglich, beispielsweise in Stahl die Form und Anordnung von Körnern, das Vorhandensein von Kristallen mit Verformungen, Fasern, Schalen, Blasen, Rissen und anderen Inhomogenitäten der Legierung zu erkennen.
Mikroskopische Methoden untersuchen die Mikrostruktur und zeigen kleinste Defekte auf. Proben werden vorläufig geschliffen, poliert und dann auf die gleiche Weise geätzt. Weitere Tests umfassen die Verwendung elektrischer und optischer Mikroskope und Röntgenbeugungsanalysen. Grundlage dieser Methode ist die Interferenz von Strahlen, die an den Atomen eines Stoffes gestreut werden. Die Eigenschaften des Materials werden durch Analyse des Röntgenbeugungsmusters kontrolliert. Die mechanischen Eigenschaften von Werkstoffen bestimmen ihre Festigkeit, die für zuverlässige und betriebssichere Bauwerke ausschlaggebend ist. Daher wird das Material sorgfältig und mit verschiedenen Methoden unter allen Bedingungen getestet, die es akzeptieren kann, ohne ein hohes Maß an mechanischen Eigenschaften zu verlieren.
Kontrollmethoden
Für die zerstörungsfreie Prüfung von Materialeigenschaften ist die richtige Auswahl effektiver Methoden von großer Bedeutung. Am genauesten und interessantesten in dieser Hinsicht sind die Methoden zur Fehlererkennung - Fehlerkontrolle. Hier ist es notwendig, die Unterschiede zwischen Methoden zur Durchführung von Fehlererkennungsmethoden und Methoden zur Bestimmung des Physischen zu kennen und zu verstehenmechanischen Eigenschaften, da sie sich grundlegend voneinander unterscheiden. Wenn letztere auf der Kontrolle physikalischer Parameter und ihrer anschließenden Korrelation mit den mechanischen Eigenschaften des Materials beruhen, basiert die Fehlererkennung auf der direkten Umwandlung von Strahlung, die von einem Fehler reflektiert wird oder eine kontrollierte Umgebung durchläuft.
Das Beste ist natürlich die komplexe Steuerung. Die Komplexität liegt in der Bestimmung der optimalen physikalischen Parameter, die verwendet werden können, um die Festigkeit und andere physikalische und mechanische Eigenschaften der Probe zu identifizieren. Und gleichzeitig wird ein optimales Maßnahmenpaket zur Beherrschung von Strukturmängeln entwickelt und anschließend umgesetzt. Und schließlich erscheint eine ganzheitliche Bewertung dieses Materials: Seine Leistung wird durch eine ganze Reihe von Parametern bestimmt, die zur Bestimmung zerstörungsfreier Methoden beigetragen haben.
Mechanische Prüfung
Mit Hilfe dieser Tests werden mechanische Eigenschaften von Materialien geprüft und bewertet. Diese Art der Kontrolle ist vor langer Zeit aufgetaucht, hat aber immer noch nicht an Relevanz verloren. Auch moderne Hightech-Materialien werden von Verbrauchern oft und heftig kritisiert. Und das legt nahe, dass die Untersuchungen sorgfältiger durchgeführt werden sollten. Wie bereits erwähnt, können mechanische Tests in zwei Arten unterteilt werden: statische und dynamische. Erstere prüfen das Produkt oder die Probe auf Torsion, Zug, Druck, Biegung, letztere auf Härte und Schlagzähigkeit. Modernes Equipment hilft, diese nicht allzu einfachen Eingriffe mit hoher Qualität durchzuführen und alle betrieblichen Probleme zu erkennen. Eigenschaften dieses Materials.
Zugversuche können die Beständigkeit eines Materials gegenüber den Auswirkungen einer konstanten oder zunehmenden Zugspannung aufzeigen. Die Methode ist alt, erprobt und verständlich, wird schon sehr lange angewendet und ist immer noch weit verbreitet. Die Probe wird entlang der Längsachse mittels einer Vorrichtung in der Prüfmaschine gedehnt. Die Zuggeschwindigkeit der Probe ist konstant, die Belastung wird durch einen speziellen Sensor gemessen. Gleichzeitig wird die Dehnung sowie die Einh altung der aufgebrachten Belastung überwacht. Die Ergebnisse solcher Tests sind äußerst nützlich, wenn neue Designs erstellt werden sollen, da noch niemand weiß, wie sie sich unter Last verh alten werden. Nur die Identifizierung aller Parameter der Elastizität des Materials kann darauf hindeuten. Maximale Spannung - die Streckgrenze definiert die maximale Belastung, der ein bestimmtes Material standh alten kann. Dies hilft bei der Berechnung der Sicherheitsspanne.

Härtetest
Die Steifigkeit des Materials errechnet sich aus dem Elastizitätsmodul. Die Kombination aus Fließfähigkeit und Härte hilft dabei, die Elastizität des Materials zu bestimmen. Wenn der technologische Prozess solche Vorgänge wie Räumen, Walzen, Pressen enthält, ist es einfach notwendig, das Ausmaß der möglichen plastischen Verformung zu kennen. Bei hoher Plastizität kann das Material unter der entsprechenden Belastung jede Form annehmen. Ein Kompressionstest kann auch als Methode zur Bestimmung des Sicherheitsabstands dienen. Besonders wenn das Material zerbrechlich ist.
Härte wird getestet mitIdentator, der aus einem viel härteren Material besteht. Am häufigsten wird dieser Test nach der Brinell-Methode (eine Kugel wird eingedrückt), Vickers (ein pyramidenförmiger Identer) oder Rockwell (ein Kegel wird verwendet) durchgeführt. Ein Identifikator wird mit einer bestimmten Kraft für eine bestimmte Zeit in die Oberfläche des Materials gedrückt und dann der auf der Probe verbleibende Abdruck untersucht. Es gibt andere ziemlich weit verbreitete Tests: zum Beispiel für die Schlagfestigkeit, wenn die Widerstandsfähigkeit eines Materials im Moment der Aufbringung einer Last bewertet wird.